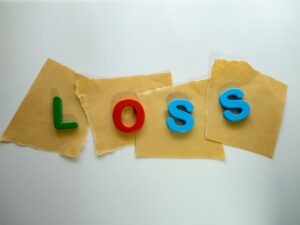
ロス
8つのムダ
8つのムダをプロセスから排除するとしていますが、ムダとは…。プロセスの中では時間、リソース(人、モノ、金)、スペースが必要ですが、お客様に届ける製品やサービスに対して価値を与えないすべての活動のことです。代表的なのはトヨタが定義した「7つのムダ」です。ここでは8つとしています。リーンシックスシグマでは、これはもともとの7つのムダに加えて8つ目のムダ(人を活用しないムダ)を付け加えました。それら8つのムダ一つ一つの言葉の頭文字を並べて、「DOWNTIME」(ダウンタイム)としています。それぞれ見ていきましょう。
DOWNTIME
「D」はDefect:不良・欠陥を作りだすこと
「O」はOver-Production:作りすぎること
「W」はWaiting:(ワークが)待たされていること
「N」はNon-Utilized Tarent:従業員の能力を活用しないこと
「T」はTransportation;運搬すること
「I」はInventory:必要のない在庫
「M」はMotion:(人の)動作
「E」はExtra Processing:価値の無い(ムダな)加工をすること
8つのムダを排除、どこから?
プロセスからムダを排除するとなると、改善プロジェクトを立ち上げて実行する必要があります。しかし、まずは私達の身の回りからムダを出さない工夫をしてみましょう!
「不良・欠陥」を最小限にする
普段と違うやり方をする、標準から逸脱することにより不良・欠陥へとつながります。標準の手順に沿って作業をしているか確認することで不良・欠陥を防ぐことが可能になります。
「作りすぎる」を最小限にする
何かあったら後で困る!という考えが作りすぎることの原因になります。特に「不良・欠陥」が後工程で見つかってしまう可能性がありから、とりあえず多めに作っておこう!とか、中間の部品在庫切れを起こしてしまわないために多めに作っておこう!などが考えられます。まずは「不良・欠陥」を減らすところから始めると、「作りすぎる」ことが減ってきます。
「(ワークが)待たされる」
先入れ先出しが徹底されていなかったり、2つ以上の作業を同時に進めることで「ワーク」が待たされます。「ワーク」は作業をする人が、一旦手を付けたら最後まで、連続でその「ワーク」に携わっていれば待たされることはありません。一旦作業を始めたら、作業が終わり次工程へ渡せるようになるように調整できれば「ワーク」は待たされません。
「従業員の能力を活用しないこと」を最小限にする
これはマネジメントの役割になります。従業員の能力を活用するには、持っているスキルを可視化するところから始めます。どのスキルが優れていて、どのスキルが向上させる対象なのかを見極める必要があります。
「運搬すること」を最小限にする
モノや情報を動かすだけの作業は付加価値を生みません。ですが意外とやりがちです。作業スペースを確保するために在庫品を動かす、必要な書類を取り出すために資料をどけるなどがそれにあたります。まずは整理・整頓・清掃・清潔・躾。5S活動を実施します。つまり作業スペースから必要ないものを排除するところから始めます。
「必要のない在庫」を最小限にする
不必要なものが、不必要な時に、必要以上にある状態を述べています。この場合も「作りすぎる」と同様、何かあったら後で困る!という考え方に起因します。後で困る「何か」とは何でしょうか。前工程の品質の悪さでしょうか。あるいは自分の工程の品質のばらつきが大きいことからを原因とした問題でしょうか。「不良・欠陥」を減らす、つまり自分の作業品質を安定させ、「不良・欠陥」を作らないことが重要になります。
「人の動作」を最小限にする
プロセスの流れに沿って作業スペースがレイアウトされていないとムダな人の動きが発生します。運搬のところでも述べましたが、基本は5S活動を徹底することです。
「価値の無い加工をすること」を最小限にする
ここでの価値が意味するところは、顧客が定義した「価値」という意味です。作業者の視点から見た「価値」ではありません。顧客(後工程を含む)が定義した「価値」が明確になることで、このムダは最小化されていきます。
改善プロジェクトを実施する
改善プロジェクトを実施するためには、それなりの準備、組織の協力、改善プロジェクトを管理できる人が必要になります。会社で改善プロジェクトを実施したいと希望されているのであれば、是非私達の今までの経験をご活用ください。下記のお問合せからお気軽にご連絡くださいませ。
Contact Us / お問い合わせ
講師派遣などのお問い合わせは以下のフォームからお願いします。